how to optimize the assembly line
optimization
The assembly line plays an important role in industrial production. Optimizing the assembly line directly affects the quality of products and the efficiency of production. Therefore, it becomes a topic that companies must pay attention to.
1. Optimize the operation time of the first station of the assembly line, and how long it takes to put a board. This is the required input cycle time to meet the production plan volume. However, in practice, the bottleneck station's working time must be greater than the first station, and the first station must not be a bottleneck station. Therefore, the first station may not be completely invested according to the required cycle time, because the bottleneck station has slowed down its speed. Therefore, from the management point of view, it is necessary to require first-stop operators to invest at the required speed. The conveyor belt speed in the assembly line can also be used to calculate the daily output. Here is the formula for the speed of the conveyor belt:
Pitch time of the conveyor belt = day-time work/day production* (1+ defective rate)
Conveyor speed = distance between markers / pitch of the conveyor
The mark distance, the distance between the marks on the assembly line belt, expects the operator to complete the work and place it on the belt line at the speed at which the marks flow; however, the chain line is not marked and the length of the board is used. Marking distance. Why use a conveyor belt? Besides semi-manufactured items, there are also semi-mandatory operators who can perform tasks as planned. However, they do not try to speed things up. They should be calculated according to the above formula.
2. Observe which station on the assembly line is the bottleneck station:
(1) Stations that are always busy;
(2) Always pull the board back to the station;
(3) From the station, there was an interval between the original one and the next.
The above three points are visually perceptible. The second is the use of a stopwatch. The operating time is the longest of all stations.
The operating time of the bottleneck station becomes the cycle time of the actual output of the entire assembly line, and the daily production formula is as follows:
Daily production = actual work time/interval cycle time
Therefore, as long as the on-site cadres can reduce their working hours, they can significantly increase their output. For example, they can use parts to do other stations, use governance tools to save movement, improve the configuration of the operating domain, and so on. However, after the bottleneck station is solved, new bottleneck stations may appear. Therefore, this new bottleneck station will be improved. Therefore, the bottleneck station will continue to improve, and the efficiency of the entire assembly line will increase day by day.
3. Observe the cycle time at the last station of the assembly line, which is the actual output cycle time. The cycle time of this station must be equal to the bottleneck station. From this station, we can calculate the efficiency of this assembly line. The formula is as follows:
Efficiency = input cycle time/actual cycle time = working time at the first station / working time at the last station
Of course, you can use the bottleneck station's operating time to calculate, but it is always simple and practical to observe the last stop.
The number of WIP on the assembly line is equal to:
(Working time at the last stop - Working hours at the first station) * (Working hours on the whole day/Working hours at the last stop)
4. Observation of the farming rate
Activity rate = time spent on work / working hours throughout the day
The so-called movement is an effective line of work on the assembly line. The fact that the operator sits on the seat does not mean that he is at work and that he has to work on the product. Therefore, observe the operator's time at work. However, in reality, it is impossible to measure every operator for the entire day. Therefore, there is a kind of work spot-checking method to simulate measurement. In fact, from time to time, we see what the operator is doing.
5, the assembly line operator sitting on the seat does not mean that he has to work seriously, so the final is to observe the speed of each operator's job, speed is a very abstract concept, light is difficult to compare and quantify from the visual, so Establishing a standard speed in your heart is faster than it is even better. The movements are streamlined, fixed, and rhythmically performed, often with better working speeds, and vice versa. This is easier to observe.
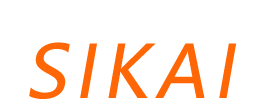
Company Profile
Yi Wu Sikai Trading Company We are a factory specializing in conveyor chains, modular belts, plastic components, and conveyor systems for 27 years. Most of our products have SGS, ISO, and CE certificates. Currently, we provide services to many big and successful companies such as Vinda, Pepsi Cola, COFCO, Pacific Can, Tech-Long and others. They are all satisfied with our products and have long-term cooperation with us. We make molds for plastic table top chains, modular belts sprockets idler wheels and other plastic components. Additionally we have a professional engineering team to design and produce conveyors according to customer requirements. Our main conveyors include spiral conveyors table top chain conveyors modular belt conveyors stainless steel chain conveyors inclined conveyors gripper conveyors etc., covering different industries such as beverages foods tissues textiles tobacco fruits batteries etc.. Our company is located in Guangzhou; you are welcome to visit us anytime.
Company
Categories
- Tel:
86-15013068448
- Skype:
- Skype:008615013068448
- Address:
- Maotan Village, Changling Road,Huangpu District, Guangzhou
Newsletter
Subscribe To Our Mailing List
subscription
QR code
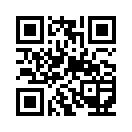